What Is A Coating Inspection?
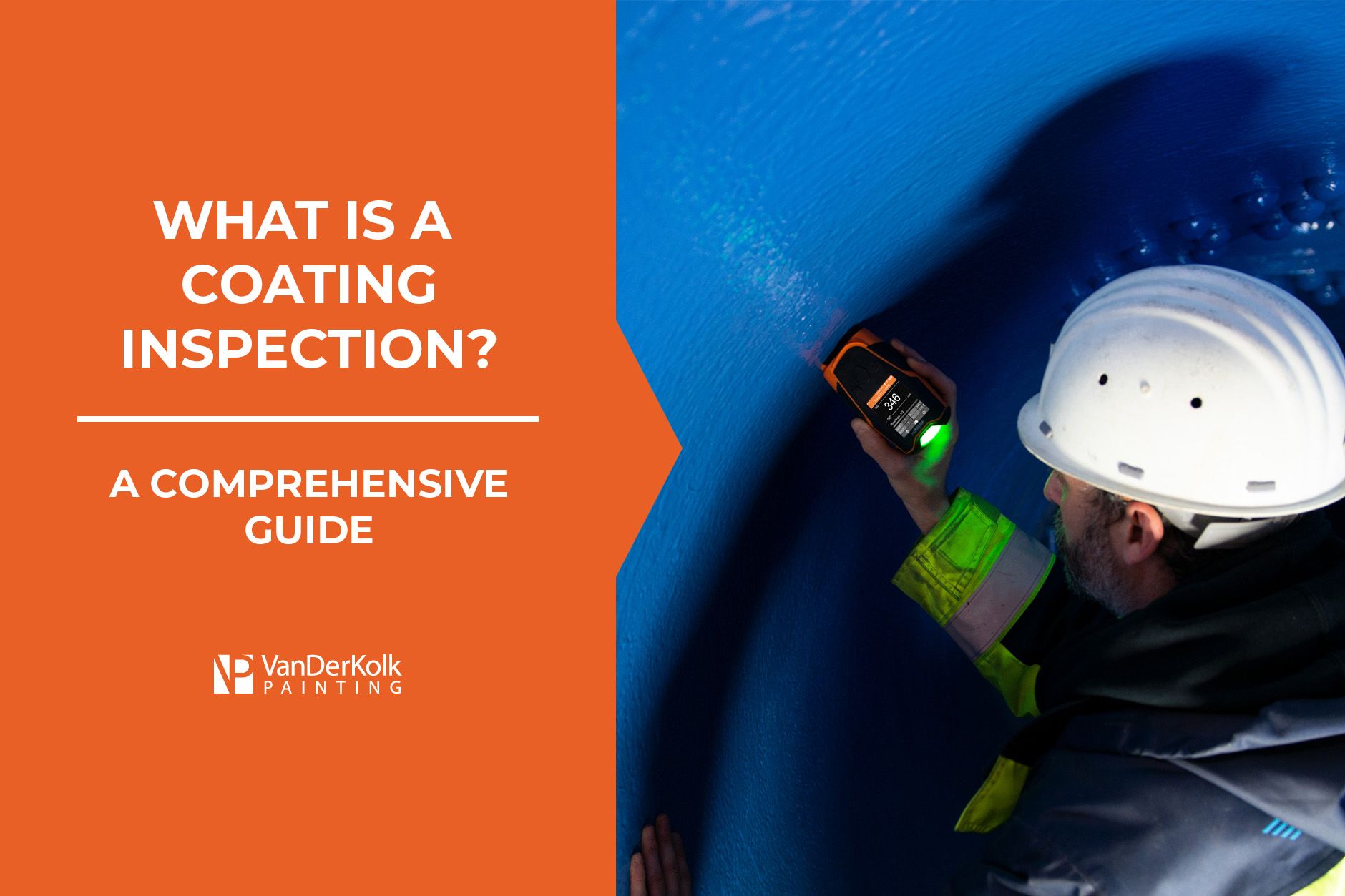
Have you ever wondered how the protective coatings on structures, pipelines, and other types of industrial machinery are monitored and maintained? The answer is through regular coating inspections.
A coating inspection, or the systematic analysis of coated surfaces, guarantees quality, efficiency, and conformity to standards. Coating inspections help to detect hidden flaws, avoid untimely breakdowns, and protect valuable assets from wear and tear. Coating inspections are a crucial quality control procedure that helps to prevent corrosion in petroleum and natural gas pipelines and maintain the appearance of architectural projects.
The experienced
commercial and
industrial painters at
VanDerKolk Painting are usually called in to apply new protective coatings for businesses after a coating inspection is performed. We’ll cover what a coating inspection is and what the process entails.
Coating Inspection Techniques
The quality and effectiveness of protective coatings depend heavily on a rigorous examination. By scrutinizing the coating's integrity and adhesion, coating inspectors can identify potential flaws, failures, or inconsistencies that might jeopardize the coating's efficacy and cause harm to the underlying mechanism.
Coating inspections can be performed in a number of different ways. There are ultimately three common techniques typically employed:
- Visual inspection
- Non-Destructive Testing
- Destructive testing
Coating inspectors often don’t exclusively rely on one technique. Several techniques may be combined for any given inspection.
Visual Inspection
A visual inspection is the first and most common step in the coating inspection process. The coated surface is thoroughly inspected for any damage or irregularities. Trained inspectors look for flaws in the covering, such as blisters, fractures, pinholes, and insufficient coverage. A visual examination is an initial step in finding problems before they escalate, allowing for prompt remedial measures or further testing.
Non-Destructive Testing (NDT)
The coating's integrity is evaluated utilizing non-destructive testing (NDT) methods that don't disturb the underlying substrate. The goal of NDT is to find flaws or irregularities that can't be seen by the human eye using various technologies.
Popular NDT methods include ultrasonic testing (UT), eddy current testing (ECT), magnetic particle testing (MT), and radiographic testing (RT). Inspectors use these methods to determine the coating's thickness, look for concealed corrosion, spot cracks, and rate the overall quality.
Destructive Testing
As the name suggests, destructive testing requires a covering or substrate to be removed or modified for a complete inspection. When a visual examination or non-destructive testing cannot provide a definitive result, this method is often used as an alternative.
Destructive testing procedures include hardness, adhesion, and salt spray testing. Testing coatings destructively reveals important information about their adhesive strength, mechanical qualities, and resilience to environmental conditions.
The Coating Inspection Process
A coating inspection aims to detect flaws, confirm the coating's quality, and ascertain whether or not it complies with applicable regulations. Here are the basic steps involved in a coating inspection, from pre-inspection to reporting.
Pre-Inspection Preparation
Coating examinations need meticulous surface preparation and must be free of impurities and prepared following coating requirements and industry norms. This rigorous process can include chemical cleaning, sandblasting, and mechanical surface profiling. Inspectors can more reliably assess the coating's adherence and spot flaws and irregularities if the surface is adequately cleaned.
A proactive inspection strategy is also essential for an orderly and thorough coating examination. The plan outlines the inspection's aims, methods, and prerequisites. Some characteristics that can be included are coating thickness, adherence, surface profile, and aesthetic appearance. The inspection plan also accounts for any relevant industry rules or project criteria that must be followed.
Execution Of Coating Inspection
You can begin the coating inspection once all preliminary work is done. In this stage, you'll implement your plan by evaluating the coated surface in great detail using specialist equipment and techniques. Here are the steps involved in a coating examination:
- First, the coated surface is visualized for flaws such as blisters, breakages, gaps, and uneven application.
- Additionally, specialized equipment like coating thickness instruments are used to measure the thickness of a coating. This prevents issues like under or over-application and guarantees compliance with stated thickness specifications.
- Furthermore, the coating's binding to the substrate is evaluated using a battery of adhesion tests, including cross-cut and pull-off procedures. Coatings must have sufficient adherence to avoid failures.
- Lastly, inspectors evaluate the coated surface's profile to guarantee it satisfies standards. Some commonly used instruments include profile depth gauges and surface profile comparators.
Inspectors will be looking for any signs of coating failures or defects during the inspection. Common coating failures and defects include:
- Abrasion
- Adhesion failure
- Alligatoring (crocodiling)
- Bleed through
- Blistering
- Bloom
- Bridging
- Bubbling
- Cathodic disbonding
- Chalking
- Checking
- Cissing
- Cobwebbing
- Cracking
- Cratering
- Crazing
- Crowsfooting
- Delamination
- Fading
- Flaking
- Grinning
- Heat damage
- Impact damage
- Intercoat contamination
- Mud cracking
- Orange peeling
- Peeling
- Pinholes
- Rippled coating
- Running coating
- Rust rashes
- Rust spotting
- Rust staining
- Sagging
- Settlement
- Skinning
- Solvent lifting
- Solvent popping
- Staining
- Stress cracking
- Undercutting
- Wrinkling
The causes and prevention techniques for each type of failure or defect mentioned above differ. An inspector will not only note the issue in a report but will also include the probable cause and suggested remedy.
Reporting and Documentation
Coating inspections rely heavily on thorough documentation and reporting since they provide the groundwork for accountability and transparency. Maintaining accurate records requires thorough documentation. The inspector will record every nuance of the coating examination so there is no space for ambiguity. This information is useful for planning future upkeep tasks like repairs and repainting. Additionally, reporting facilitates precise evaluation and analysis of inspection findings by quality control specialists.
Importance of Thorough Documentation
As a first step, the report has to include specifics like the project's location, the date and time of the inspection, and any other pertinent information. The report should include any additional information on the coating system used, such as the brand and kind of coating used and any relevant application guidelines.
The inspection report needs to provide a detailed account of the inspection methods employed, the inspection's extent, and the components examined for defects and non-conformance. To enhance the report's accuracy, photos or detailed descriptions of the current condition of the coating should be included.
Lastly, the report should conclude with suggestions for further action or follow-up based on the inspection results. Repairs, re-coating, more testing, and resolving safety and environmental issues are all possibilities. This thorough documentation allows managers to make educated decisions, take appropriate measures, and guarantee the coatings' long-term durability and performance.
Challenges In Coating Inspection
Coating inspections are complex procedures, making it challenging for the quality assurance manager to produce a precise report. Below are some of the key obstacles that cause hindrances in the inspection process.
Surface Preparation
Proper surface preparation is essential for the coating inspection. Inspectors can encounter difficulty assessing if the surface has not been adequately prepared for coating.
Environmental Factors
Coating examinations are often performed in less-than-ideal circumstances. Challenges can arise during inspections if the environment is sweltering, humid, or caustic. Coating inspectors make adjustments and take extra safety measures to carry out their inspections successfully.
Hard-To-Reach Locations
Coated surfaces are found in various environments, some of which are difficult to access due to their size or location. Inspecting coatings can be challenging in hard-to-reach locations.
Best Practices for Coating Inspection
Coating inspectors have created standards of excellence to conduct each task proficiently and accurately. There are several best practices for conducting inspections that coating inspectors should adhere to.
Create A Clear Inspection Scope
To begin, coating inspectors develop comprehensive inspection plans by defining their work and its outcomes in scope, approach, and acceptance criteria. A clearly defined scope makes planning and execution much easier.
Maintain Open Communication
Good lines of communication and teamwork are essential for effective coating inspections. The smoothness of the inspection process depends on the inspectors' ability to communicate effectively with other involved parties. Coordinating regularly reduces the likelihood of problems and boosts productivity.
Staying Up-To-Date With New Technology
Industry standards and coatings technology are constantly evolving. Coating inspectors must place a premium on keeping up with industry trends, regulations, and best practices. This allows them to adjust their inspection practices to meet current standards and guarantee the highest quality assessments.
Use A Multifaceted Strategy for Inspection
While inspecting coatings, inspectors must be open to utilizing various coating inspection techniques. This multi-pronged strategy allows for a comprehensive evaluation of coating quality, identifying probable faults or difficulties and forming reliable judgments.
Do Your Surfaces Need A New Coating?
The skilled industrial and commercial painters at VanDerKolk Painting can help you coat building surfaces and equipment with a new protective coating if you find that you need one through a coating inspection. We can coat anything in protective paint from water pipes to industrial machinery.
Our team takes great pride in offering a collaborative and transparent approach to painting services. We’ll work directly with your team to coordinate painting so that we can minimize or avoid downtime for your operations. VanDerKolk Painting offers free estimates. You can request an estimate by calling
(616) 202-6570 or by filling out an online
contact form.
Request A Free Quote
Our Services
Residential Services
Commercial & Industrial Services
Trailer & Equipment Painting
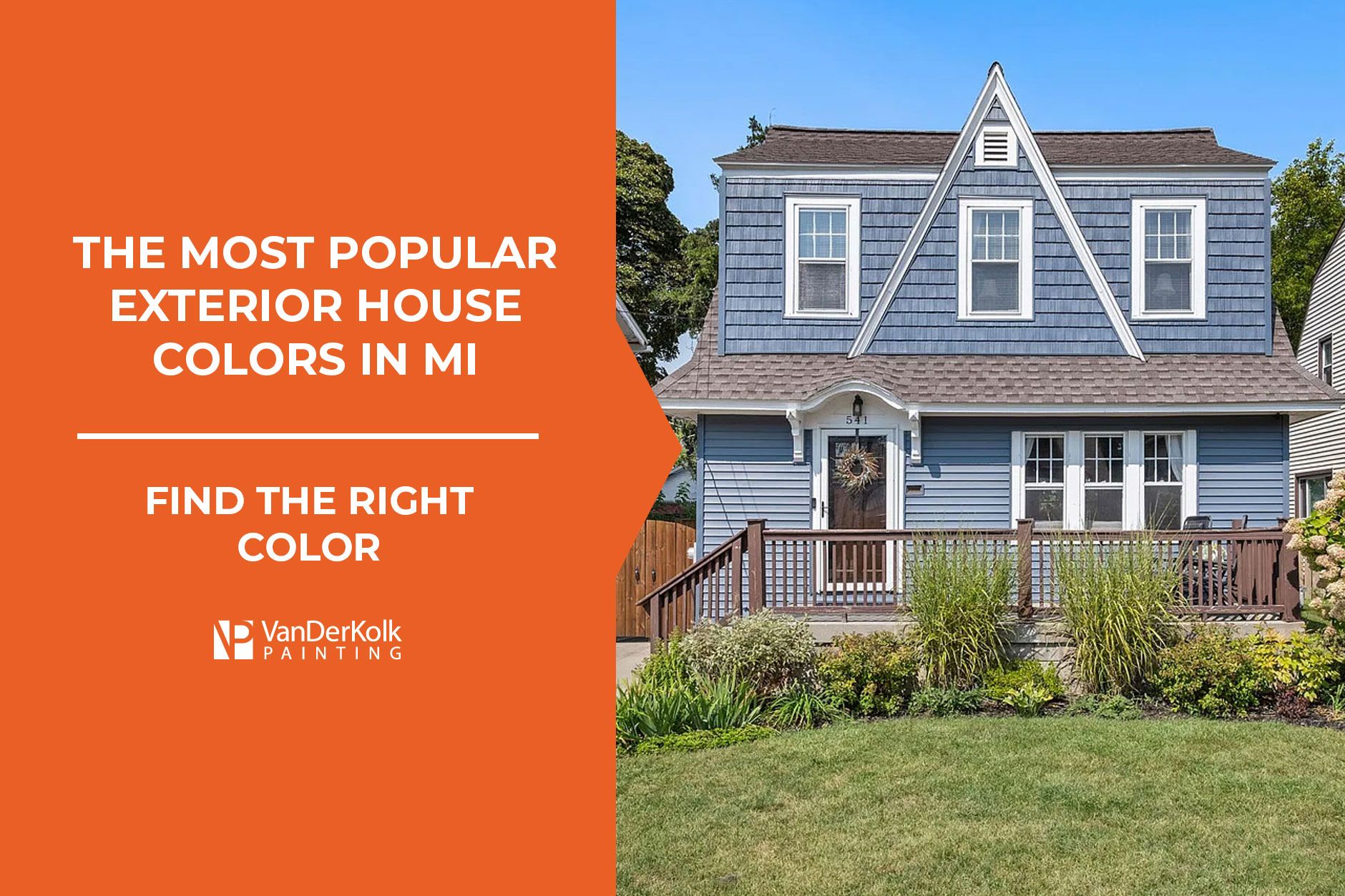
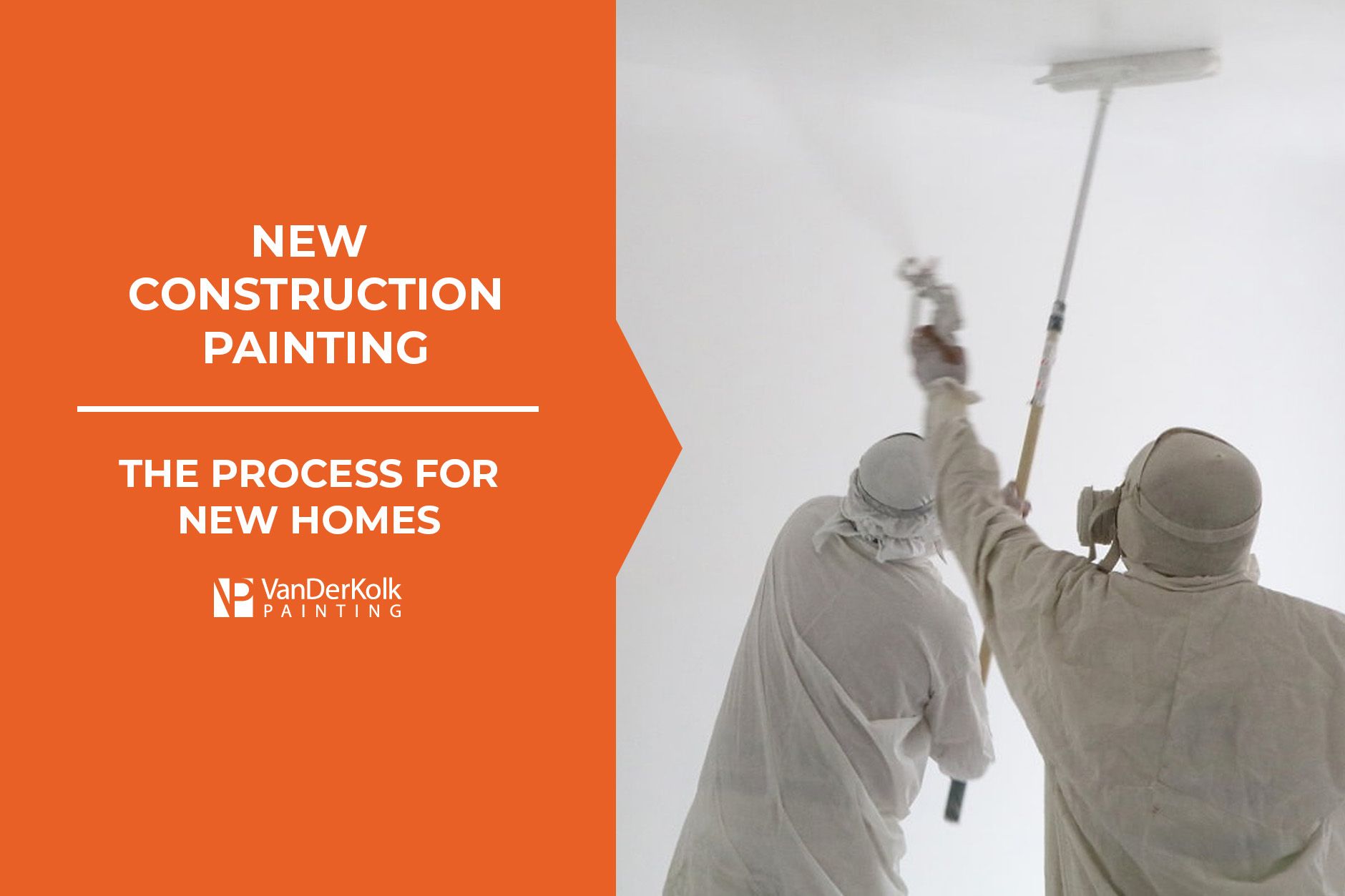
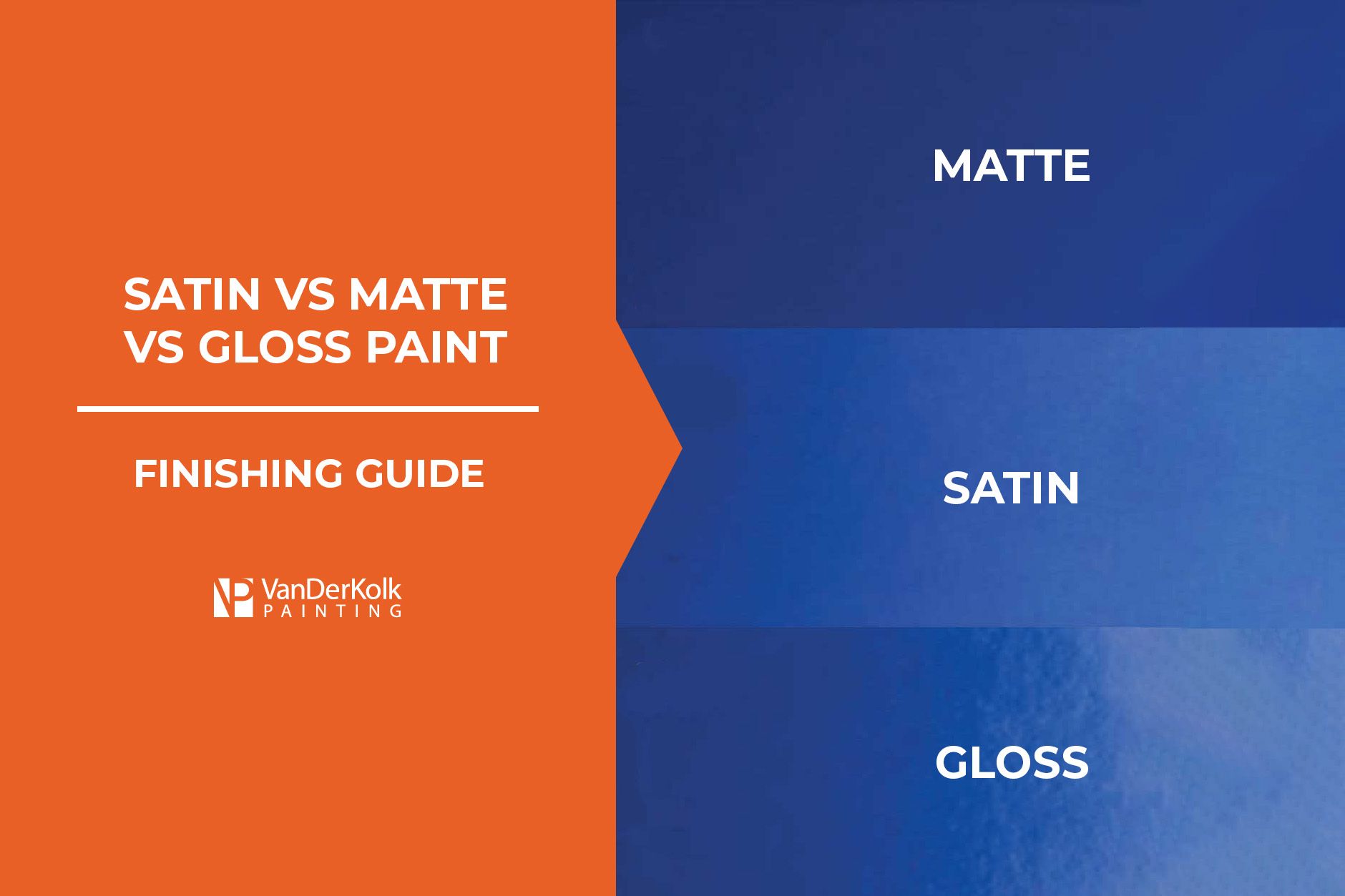
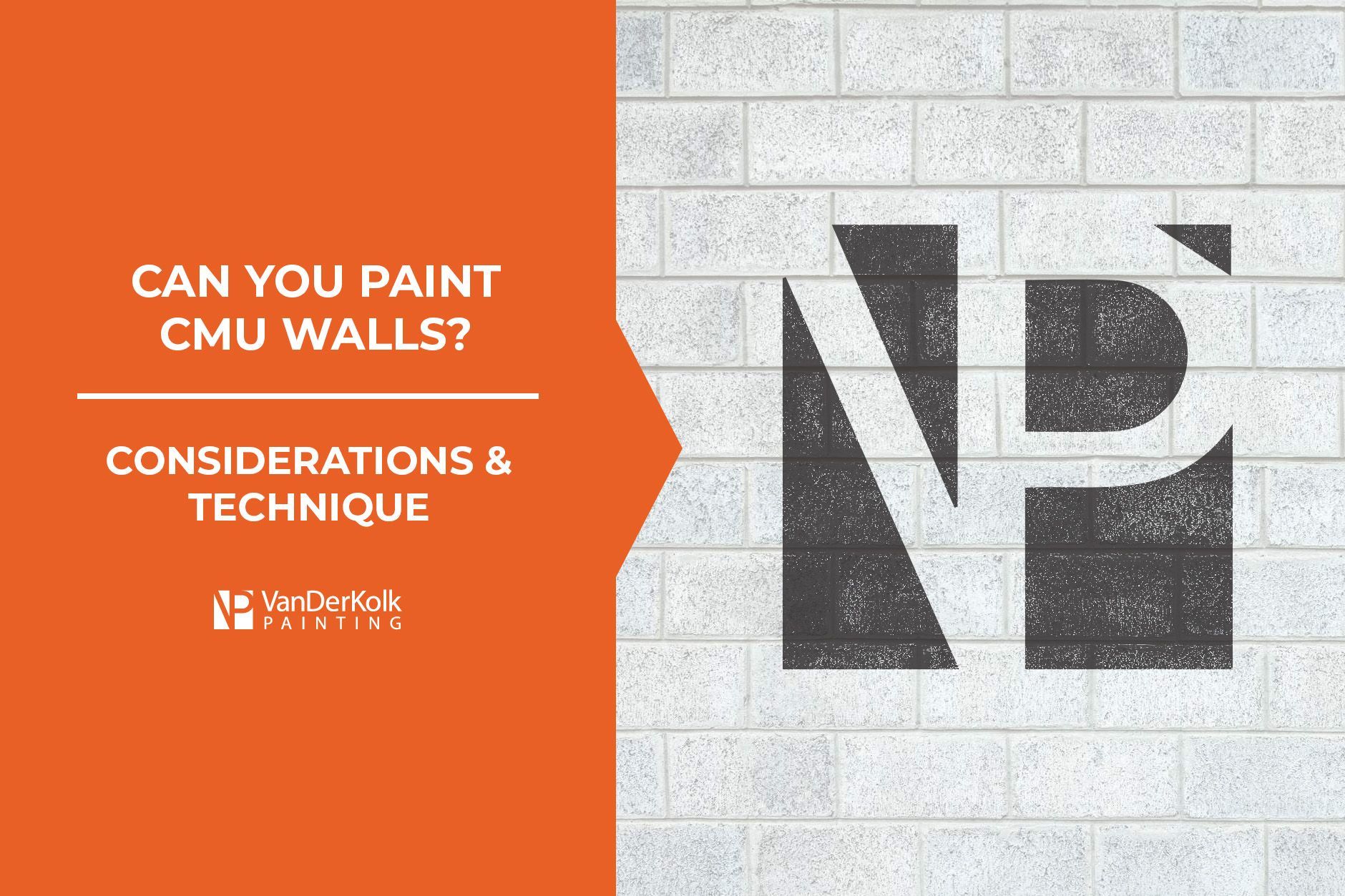
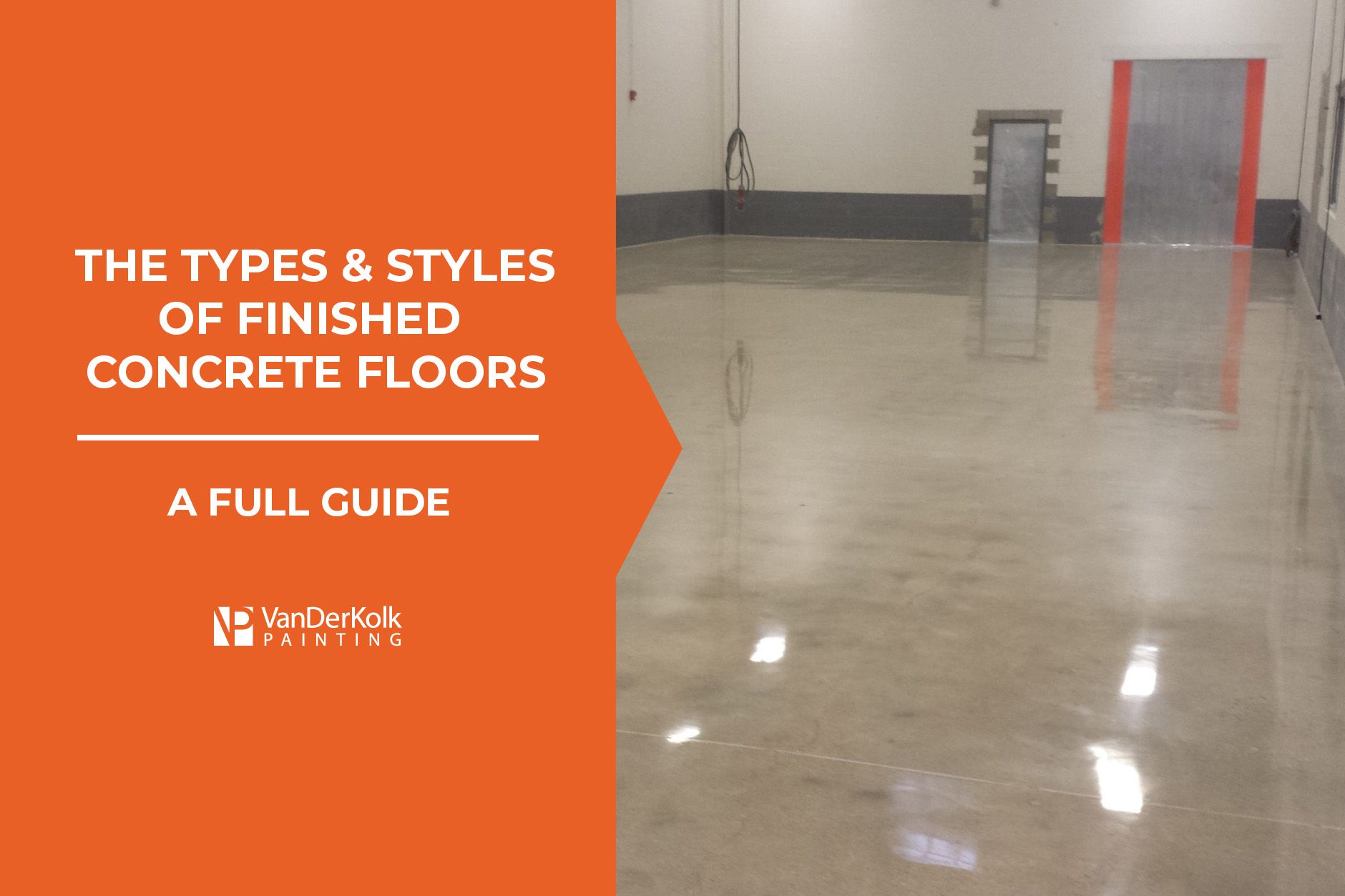
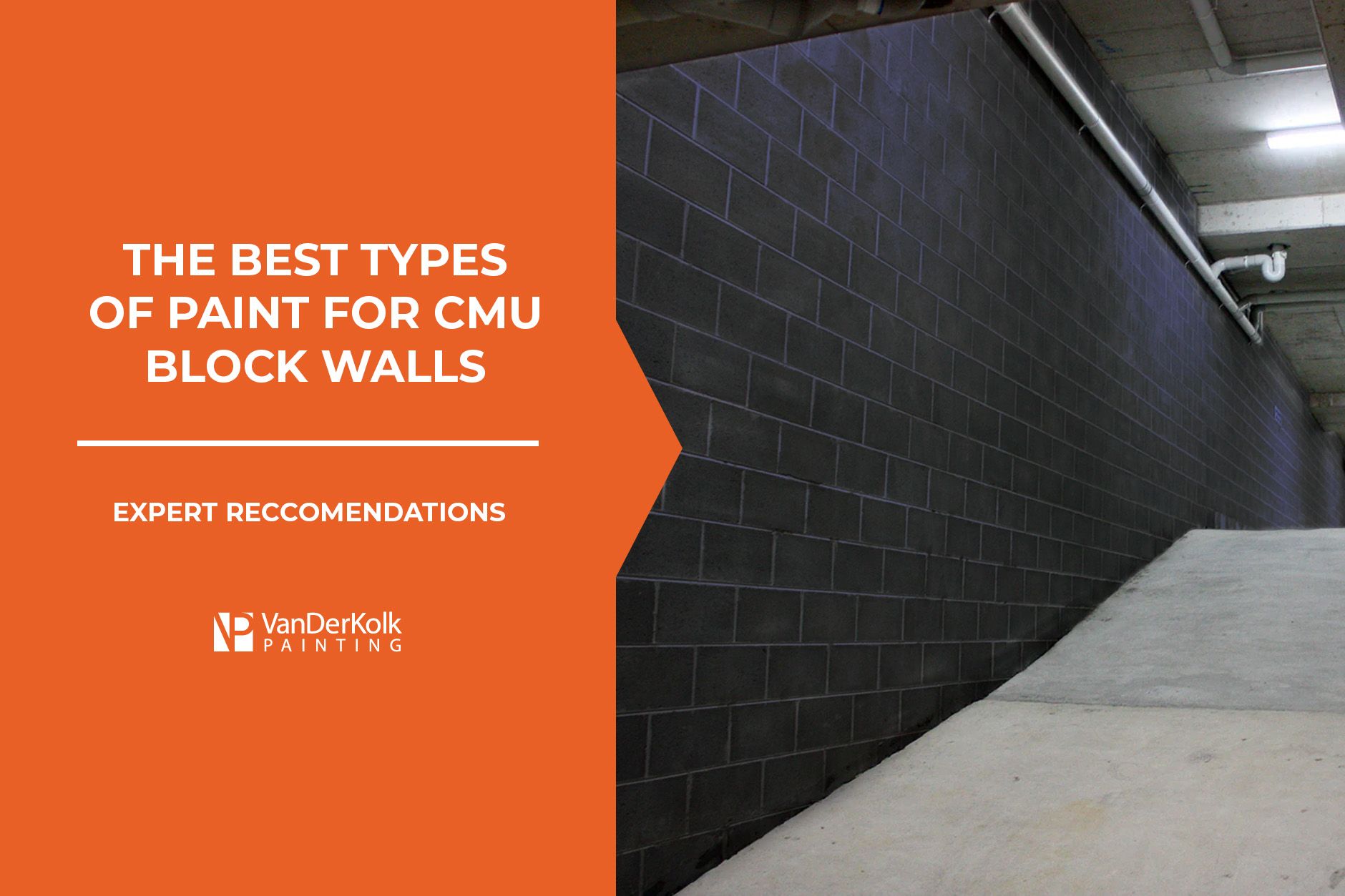
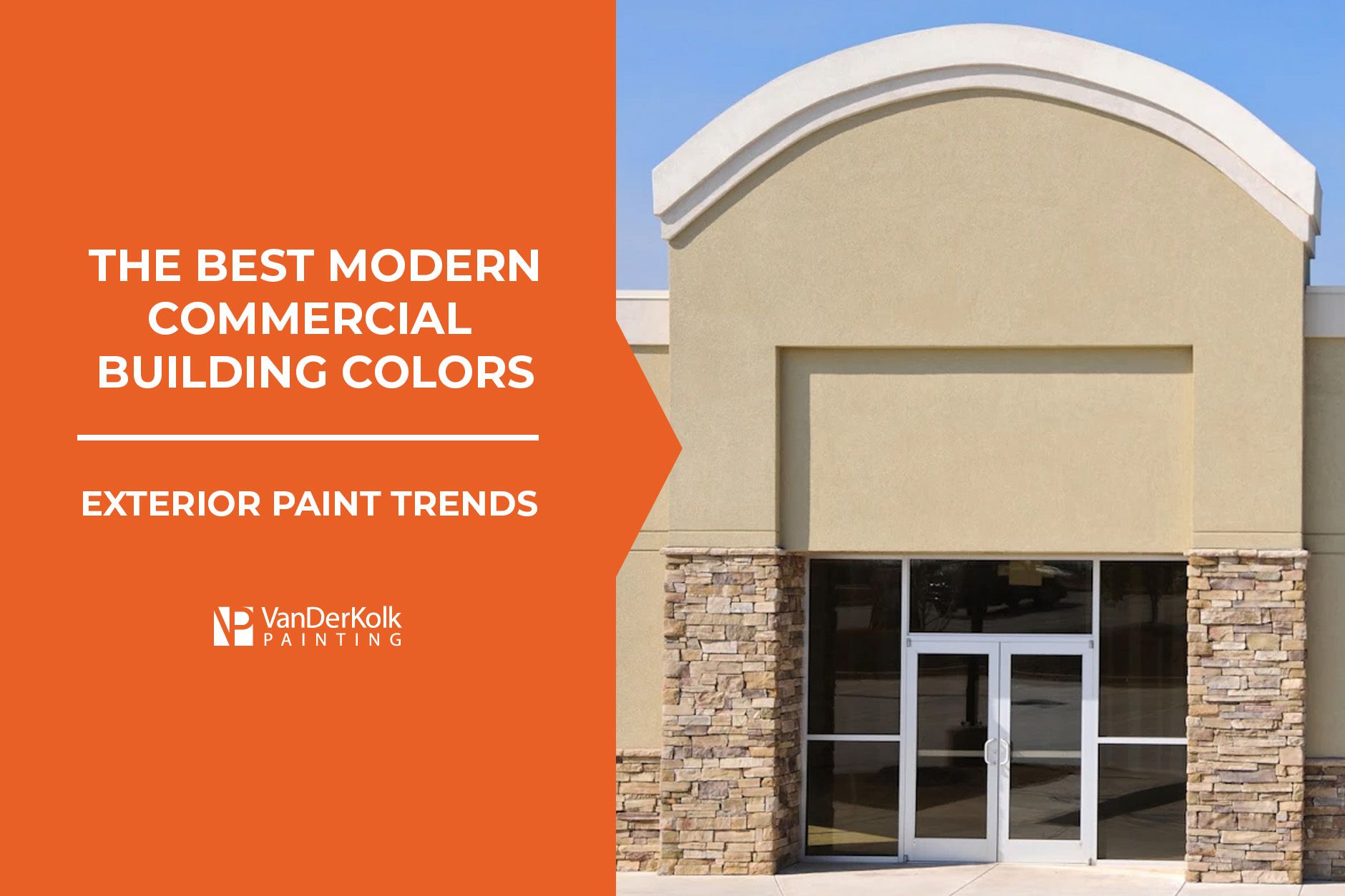
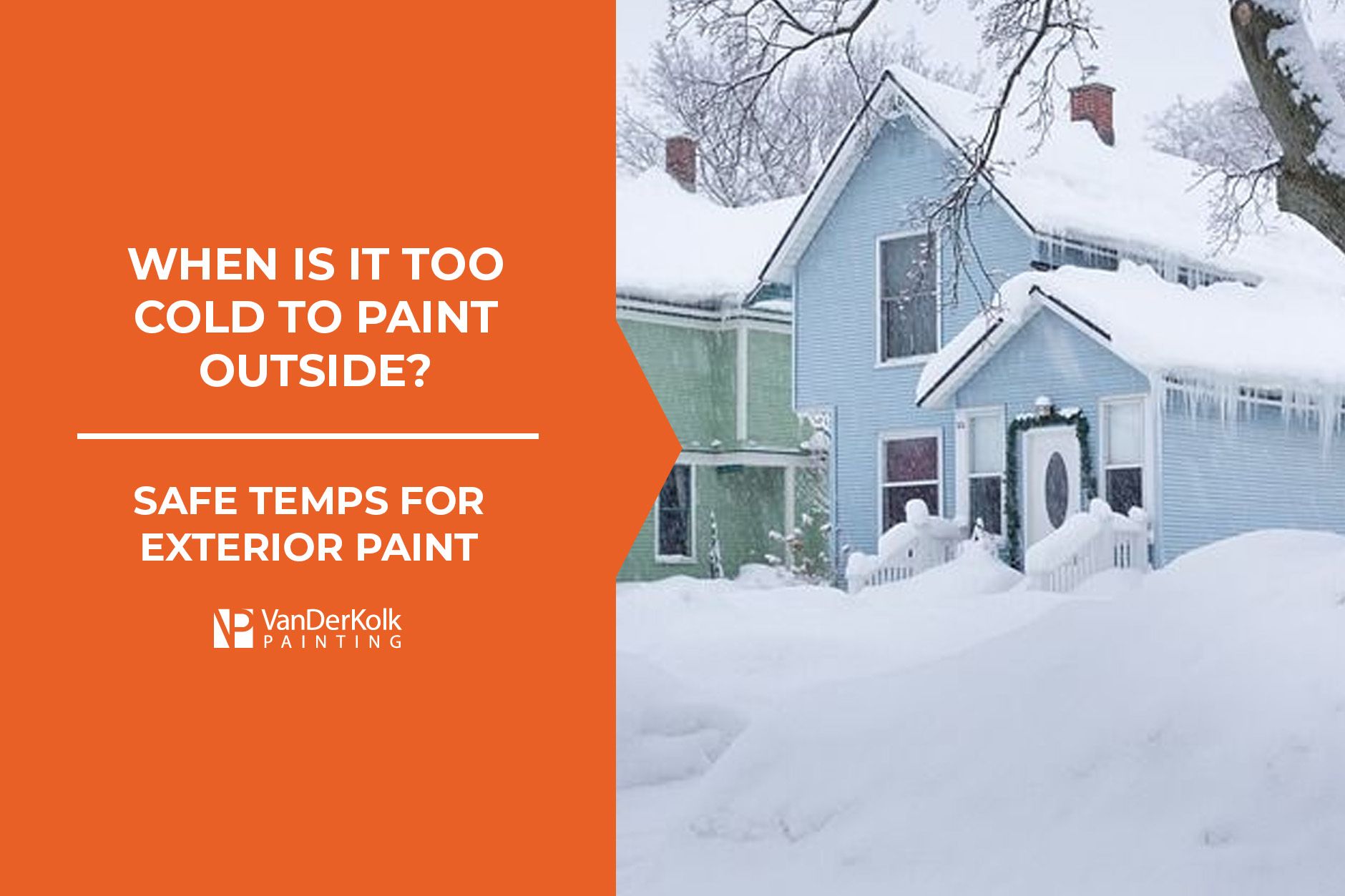
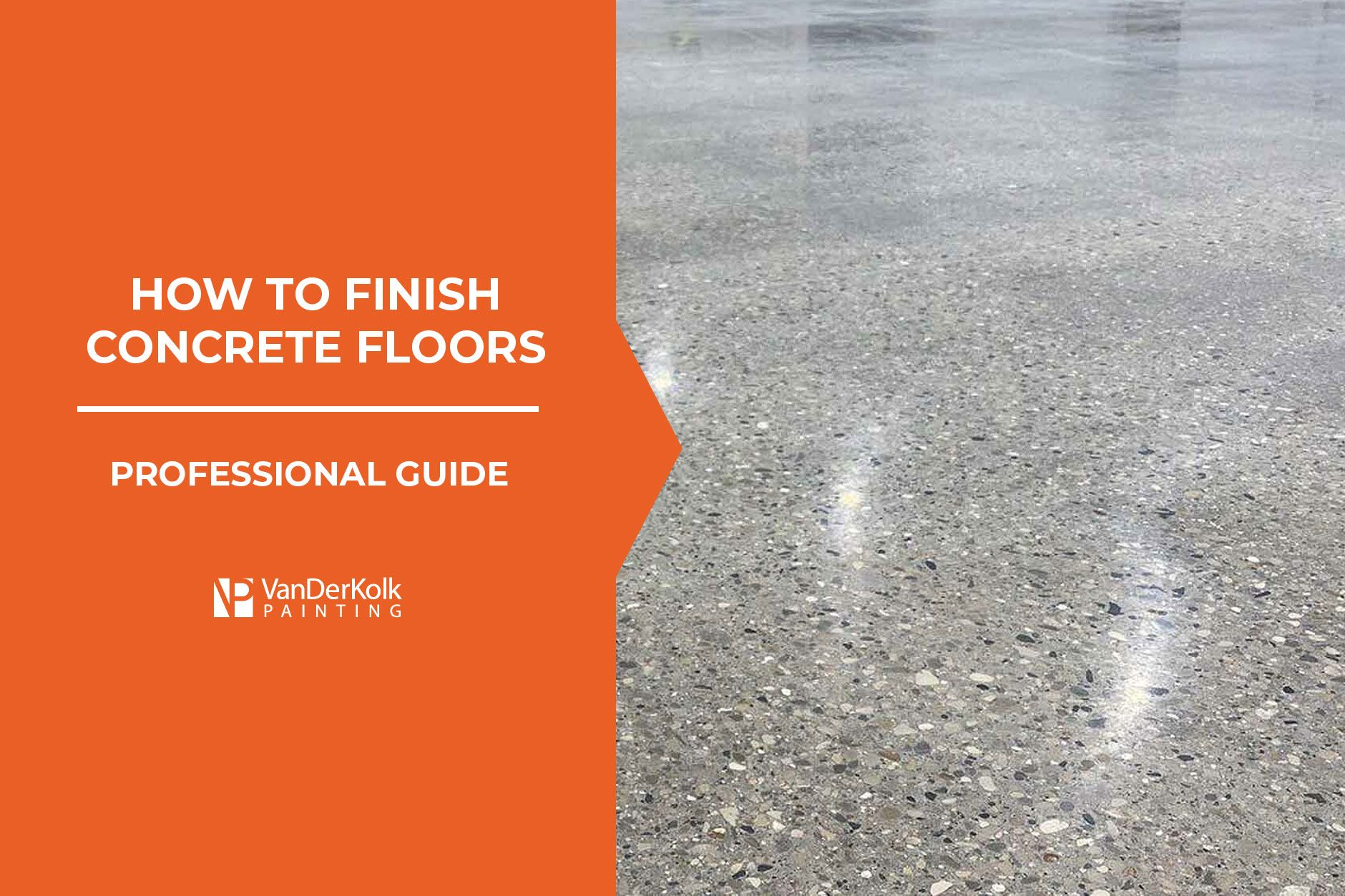
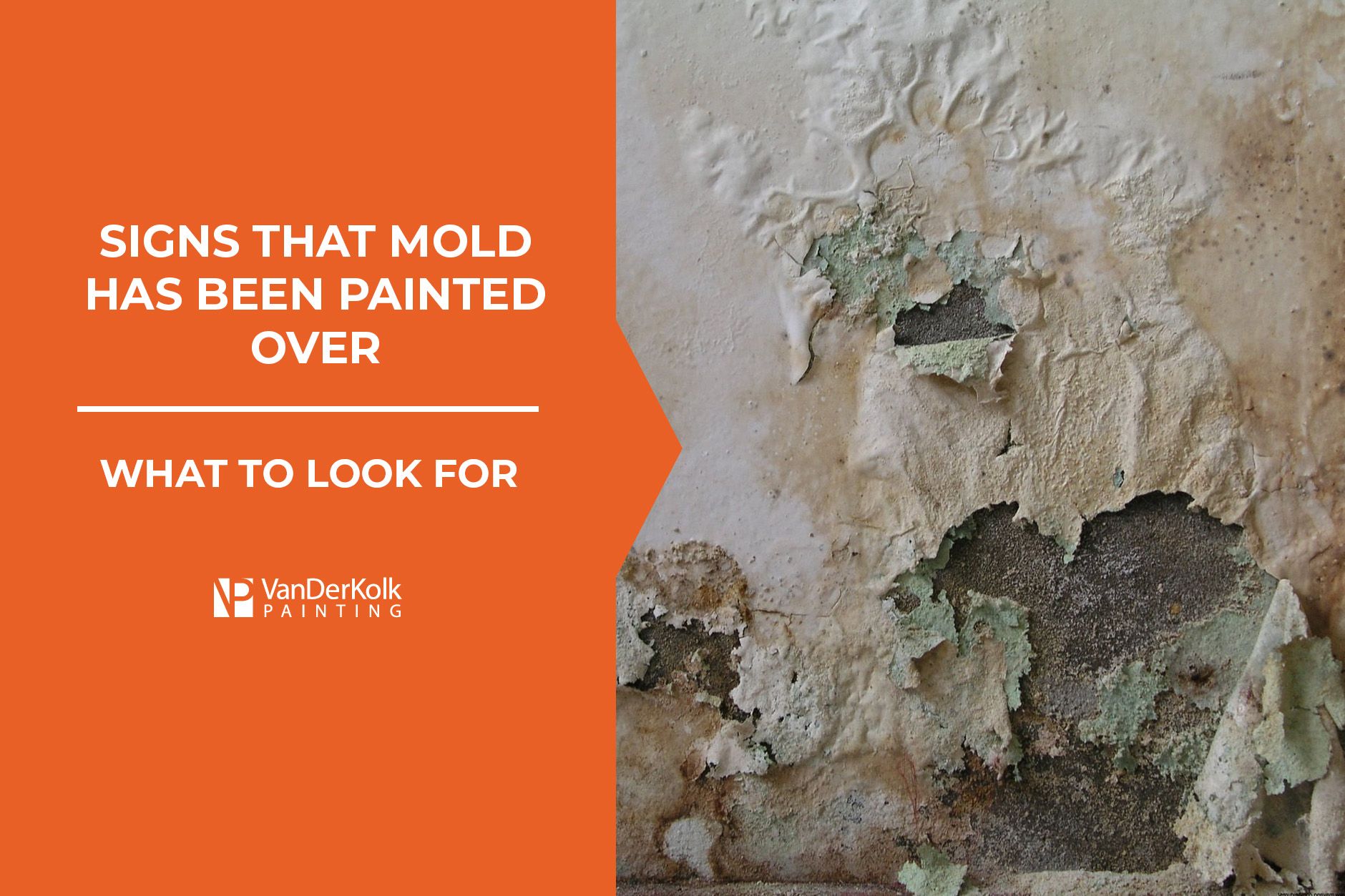